8 Technology Tune-up Tips for an Efficient, Accurate Harvest
October 12, 2018
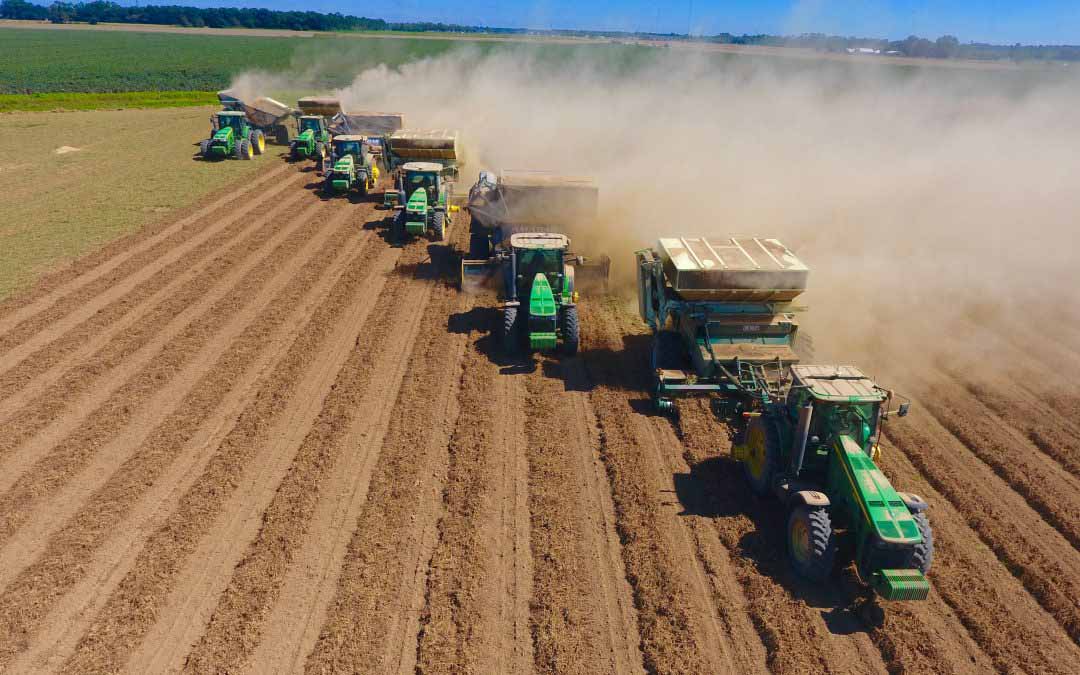
With the end of the season fast approaching, you’re probably monitoring your crops and the weather for the ideal time to get into the field and begin harvesting.
While you likely know the importance of conducting a thorough inspection of your equipment before you get the combine rolling, you should also ensure your precision technology is up-to-date and functioning correctly.
It’s key to do this now, because otherwise, you may find yourself making repairs and corrections later — when you would rather be spending that time harvesting.
Not only will a pre-harvest tune-up save on time and reduce stress, it’ll also ensure the data you’re collecting is accurate, which is crucial if you plan on using it to create prescriptions for the next season.
Here are some tips on how you can inspect and prepare your precision technology for a smooth and successful harvest.
Pre-Harvest Tune-Up: Steering Systems
1 – Start with the Steering Hardware
The first step is checking the hardware of the guidance steering system. This includes:
• Greasing all spindles and kingpins, and making sure there’s no wear in them, as that will result in a poor response in the system.
• Checking that linkages are tight and aligned properly.
• Verifying that the camber, caster and toe of your steering system are within spec, as unalignment will cause the system to pull to one side, resulting in uneven and excessive wear on your tires and potential steering errors.
• Ensuring the tires are in good shape — tread depth is within proper spec; no excessive wear or deformities. Also, be sure that they’re inflated to the proper pressure as listed in the operator’s manual.
If you have a hydraulic steering system — which most factory-installed systems are — you’ll want to make sure the hydraulic oil levels are good. Also, check that the hoses aren’t leaking and are secured in the proper locations; not falling down and getting in the way of the tires or the threshing mechanisms.
It’s also important to check that the filtering system is updated, with any filters changed according to the service time periods stated in the manual. Clogged filters cause reduced flow which in turn can cause reduced steering performance – and nobody likes that…
If you have an assisted steering system, such as the EZ-Pilot and EZ-Steer, you’ll need to make sure the anti-rotation bracketry is good and secure, which is generally on the steering column. Again, verify that the linkages and brackets are tight. No bushings or other pieces should be sloping or worn.
And if your system has a steering sensor, check the linkages on it, ensuring they’re free and clear, working properly with no sticking or slop. Cables should be routed properly and not hanging. If you find any wearing or broken wires, repair and replace them as required per the service manual.
2 – Do a Test Run
After you’ve checked all the physical aspects of the steering system, you’ll want to do a test run.
But first, if you transferred the GPS guidance system from another piece of equipment — such as your tractor or sprayer — to your combine, make sure the right vehicle is entered into the system, so you have the right dimensions and configurations set up.
Once you’ve confirmed the configurations are correct, set an AB line in the field and see if the system steers to it and is providing good performance. You’ll need to do this with the header on and threshing mechanism engaged as this can change the dynamics of the system.
Also, verify that the steering angle in your display matches the angle of your tires. For example, if you turn your wheels to the left and the display says the angle is 27 degrees, draw a line in the ground from the tire and calculate whether the actual angle is within a couple degrees of that.
If you’re not seeing a good performance from the test run, start with the basics: Verify measurements and orientations of precision ag equipment – more often than not inches became feet or vice-versa. You can also do the corresponding calibrations for the system over again per the installation manual.
But if you’re not familiar with this process or not comfortable doing it, you may want to contact your precision ag dealer to redo the calibrations for you or verify the setup is correct.
3 – Reactivate GPS Subscriptions
If you have a GPS subscription that needs reactivating for harvest, this is also the time to contact your service provider and get it back up and running. There is usually a little lead time to get it reactivated, so it’s better to get this done now so you know it’ll be ready to go for the timeframe you expect to be harvesting.
4 – Do a Data Cleanup
After conducting a full inspection of the steering hardware and testing that it works properly, you’ll want to do a data cleanup of your guidance lines so that only the ones you need are available. This is especially important if you have custom or hired help that will be using the system, as it helps ensure they’ll choose the right line.
If you have a bunch of guidance lines in your system and you’re not sure what they do, it’s best to just get rid of them.
Also, consider whether you’ve changed landowners, have acquired new land or have renamed any land, as this is also the time to redo an export out of your ag management software so that your field structures are up to date for proper data collection.
Aim to have everything set up properly so that you’re most likely to succeed in getting in the right field at the right time.
Pre-Harvest Tune-Up: Yield Monitors
5 – Calibration Key for Accurate Yield
Our yield monitoring systems are volume-based, which means it senses the amount of crop that sits on the paddle in the grain elevator. So the first step in collecting accurate data is to teach the system what the zero point is — what does the paddle look like with nothing on it?
Because the paddles can wear and change shape over time, this affects how much volume the sensor reads.
You’ll also need to decide whether you’ll keep or delete the load data from the previous season for calibrating this season’s yield.
If you’re harvesting a different crop, it’s likely going to need its own calibration. For example, if last year you harvested wheat and now you’re harvesting corn, the grain is different and the grain flows are likely different as well. So you’ll probably need two separate calibrations.
You’ll also need to factor in whether the yield potential is similar. If the last wheat crop you harvested was hailed out, its grain flow would’ve been much lower. If your wheat crop this year is normal, the calibration won’t be tailored for a much higher grain flow.
That also means that if you’ve got a crop that has some sort of stress, it may not produce as much yield as the previous season, so you’re probably going to have to calibrate it to this year’s crop.
6 – Harvest for Accurate Data
To calibrate for this year’s crop you’ll need new data in the system before you can apply offsets to it, which means you’ll need to do some harvesting to correct the system.
We recommend harvesting at least four loads to get an accurate calibration curve. What is considered one load depends on the machine and operator — for some, it may be how much it takes to fill the combine grain tank, for others, it may be how much it takes to fill a semi.
The loads also need to be taken at various speeds so the system can get a sense for different crop flows to create an accurate calibration curve. If you take all your loads at the same grain flow, you’ll only get one point on the curve.
While you can do more than four loads, we don’t recommend going above six or seven, as it likely won’t make much of a difference in the accuracy of the calibration.
7 – Troubleshooting Calibrations
If you decided to keep your old load data for calibrations and you start to see inaccuracies, inputting new loads is not likely to help — instead it’s only going to skew your numbers.
You can try to patch it, but more importantly, you should stop, take a look at the machine and figure out what’s wrong. Know that if you need to change something, you might have to get some new calibration loads to reset the data.
Many problems that come up on the yield monitor often indicate a problem with the combine itself. This primarily includes cleaning the elevator and making sure the chain and paddles are in good shape.
Another consideration to keep in mind is that without a scale ticket, you can’t offset your yield data, which means the information the system is collecting may not be 100% accurate. You’ll still know the high and low points in your fields, but the numbers won’t be relative until you have that information.
But once you do have your scale tickets, you can always go back into the system and apply that information to correct the data later.
Learn more about how a Trimble yield monitor can help you capture valuable data that will enhance your decision-making for next season and beyond.
Start Early
The sooner you can start on this process, the better. Try to do this at least a couple weeks to a month in advance of when you plan on harvesting, that way if you need to order parts or make major repairs, you’ve given yourself enough time to get that taken care of.
The other benefit to doing this early is that you can teach others on your operation how to work the systems and troubleshoot problems. That way if you find yourself in a situation where someone else needs to step in, you can rely on them to get the job done. It’s much easier to teach others these things when you’re not under stress yourself.
If you’re not comfortable inspecting and maintaining the precision side of your pre-harvest maintenance, look for precision ag companies or a precision technician at your dealer that may offer a maintenance service to do this for you. Costs for this kind of service may be anywhere between $150 and $500, plus any additional expenses for parts and repairs.
Remember, your data is only as good as the machine itself. If something isn’t working properly, you’re probably not collecting accurate data, which can have big consequences for future growing seasons.
Photo Credit: Chip Bryars, Vantage South
Authors: Dwight Easterly and Zach Gettman
Zach Gettman is a Product Manager for Trimble and manages the development of solutions worldwide. With 10 years of experience, specializing in flow and application control systems, he aims to help farmers increase their efficiency in the field.
Dwight Easterly is a Field Applications Engineer for Trimble, helping farmers improve efficiency and productivity on their farms with the proper installation of precision ag technology.